Các nhà tích hợp hệ thống phải đối mặt với những thách thức chung khi kết hợp thiết bị của nhà sản xuất thiết bị gốc (OEM) vào các dự án tự động hóa, nhưng có một số chiến lược đã được chứng minh thực tiễn để thúc đẩy thành công.
Sử dụng thiết bị trong khuôn khổ do các nhà sản xuất thiết bị gốc (OEM) cung cấp là điều phổ biến trong ngành nước / nước thải (xem Hình 1). Tuy nhiên, thiết bị OEM có thể tạo ra một số thách thức cụ thể đối với nhà tích hợp hệ thống System Integrator (SI) chịu trách nhiệm về phần tự động hóa của dự án, đòi hỏi phải có một cách tiếp cận chiến lược để thúc đẩy sự phù hợp với các thành phần, hệ thống và tiêu chuẩn khác có thể thay đổi so với cung cấp OEM tiêu chuẩn. Bài viết này khám phá những thách thức này và mô tả các chiến lược để thúc đẩy thành công.
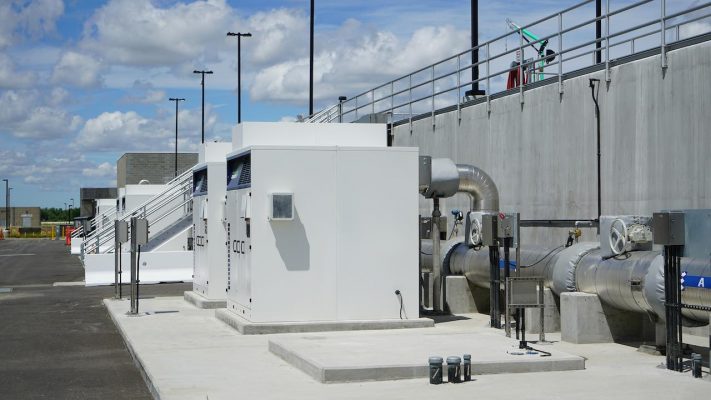
Nội dung chính
Ba thách thức tích hợp hệ thống OEM
Những thách thức liên quan đến tích hợp hệ thống OEM có thể được phân loại thành ba lĩnh vực riêng biệt:
- Tương phản các tiêu chuẩn về công nghệ và yêu cầu cấu hình
- Công nghệ quy trình mới
- Điều phối nhóm dự án (xem Hình 2).
Tương phản các tiêu chuẩn trong yêu cầu công nghệ và cấu hình. Có nhiều lĩnh vực mà thiết bị OEM có thể khác với thiết bị “không bao gồm” được xác định cho hệ thống điều khiển bao gồm bộ điều khiển logic khả lập trình (PLC), thiết bị đầu cuối giao diện người vận hành tại chỗ (OIT), giao thức truyền thông và các tiêu chuẩn phần mềm PLC và OIT (xem Hình 3).
Có một số lý do khiến nền tảng PLC được chọn cho cân bằng của nhà máy (BOP) có thể không phù hợp với PLC của OEM. OEM có khả năng kinh nghiệm với một số nền tảng PLC nhất định và thường thiết bị OEM được chọn cho một công nghệ quy trình cụ thể chứ không phải tự động hóa. Thiết bị OEM cũng có thể được chọn làm phần cốt lõi của thiết kế trước khi lựa chọn nền tảng BOP PLC.
Những thách thức của OIT được chọn cho thiết bị OEM thường giống với những thách thức liên quan đến lựa chọn PLC của OEM. OIT của OEM thường không phải từ cùng một nhà cung cấp như phần mềm hệ thống kiểm soát giám sát và thu thập dữ liệu (SCADA) cho BOP. Độ phân giải màn hình với OIT thường thấp hơn so với ứng dụng phần mềm SCADA hiện đại được phát triển để chạy trên màn hình lớn có độ phân giải cao; đồ họa OIT nhỏ hơn và đơn giản hơn những gì sẽ được phát triển ở cấp ứng dụng SCADA.
Ngoài các nền tảng phần cứng, những thách thức bổ sung khác thường được đưa ra bao gồm sự khác biệt về giao thức truyền thông, mô hình bảo mật và phương sai của giao diện người-máy (HMI) và các tiêu chuẩn phần mềm PLC.
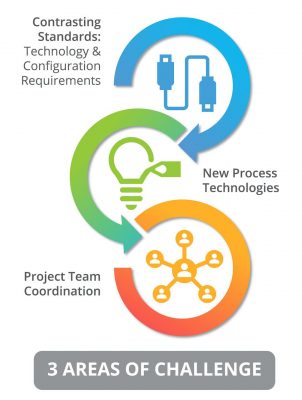
Các giao thức truyền thông khác nhau cũng phải được điều chỉnh. Có một số cách để làm điều này nhờ các thiết bị đã được phát triển để giải quyết vấn đề này trong các hệ thống điều khiển hiện đại. Các thiết bị này đã phát triển theo thời gian để cho phép công nghệ cũ được tích hợp với công nghệ mới hơn và để thiết bị từ các nhà sản xuất khác nhau giao tiếp trong một hệ thống điều khiển duy nhất. Thiết kế cần được phân tích để xác định xem các thiết bị cho phép các PLC thiết bị OEM khác nhau giao tiếp với phần còn lại của hệ thống có phù hợp để đưa vào hay không. May mắn thay, có một giải pháp có thể được tận dụng nếu có sự sơ suất được xác định trong thiết kế.
Phương sai tiêu chuẩn phần mềm PLC và HMI có thể rất khó giải quyết, chủ yếu là do các tiêu chuẩn phần mềm chủ quan hơn nhiều so với các phương pháp xác định như giao thức truyền thông.
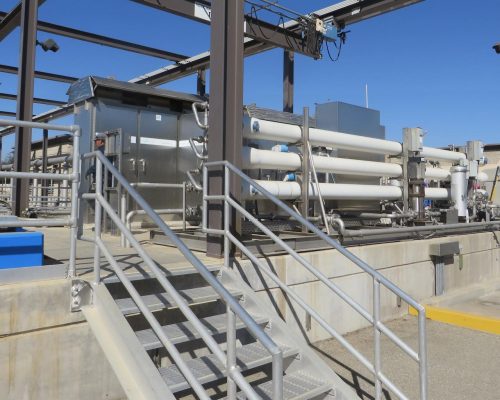
Các tiêu chuẩn cho hệ thống BOP có thể đến từ một số nguồn bao gồm người dùng cuối, tài liệu kế hoạch và đặc điểm kỹ thuật, nhà sản xuất nền tảng phần mềm, hội thảo lập trình hoặc các thành viên nhóm hợp đồng bổ sung (xem Hình 4).
OEM thường đưa ra các tiêu chuẩn mà họ có thể cung cấp như một giải pháp loại bỏ cookie để giữ chi phí thấp trong khi vẫn đáp ứng các yêu cầu cài đặt khác nhau của ngành. Các tiêu chuẩn được OEM sử dụng thường được phát triển nội bộ với nhóm nhân viên phần mềm của riêng họ, tập trung vào chức năng quy trình và các yếu tố khác không và không thể xem xét đến hệ thống kiểm soát BOP tổng thể.
Những yếu tố này có thể gây ra sự sai lệch giữa tiêu chuẩn phần mềm OEM và tiêu chuẩn được xác định cho BOP. Sự khác biệt có thể từ nhỏ như danh mục cảnh báo chính như trạng thái màu đối lập với tiêu chuẩn BOP. Các tiêu chuẩn cần được đánh giá và kết hợp vào kế hoạch lớn hơn cho thiết kế phần mềm tổng thể. Nỗ lực này thường thuộc về SI vì họ giữ vị trí quan trọng để giúp cung cấp các giải pháp bằng cách sử dụng quan hệ đối tác hợp tác với các nhà tư vấn, kỹ sư thiết kế và người dùng cuối.
Quy trình công nghệ mới
Có nhiều công nghệ và cải tiến đang phát triển. Việc hiểu rõ ứng dụng của các công nghệ này, các biến quá trình đang được giám sát, các chiến lược kiểm soát đang được sử dụng và các cảnh báo quan trọng cho mỗi hệ thống là điều bắt buộc. Điều này cho phép SI tích hợp thiết bị OEM một cách hiệu quả vào một mô hình phần mềm lớn hơn bao gồm toàn bộ hệ thống điều khiển BOP.
Việc nắm chắc công nghệ quy trình cụ thể được sử dụng bởi từng OEM cần có thời gian và yêu cầu nghiên cứu nội bộ thường bị bỏ qua khi lịch trình nguồn lực kỹ thuật được phát triển. Các quyết định được đưa ra liên quan đến việc tích hợp thiết bị vào hệ thống điều khiển BOP sẽ hiệu quả hơn nếu nhà tích hợp có thể hiểu công nghệ quy trình của OEM và giao tiếp với nhóm đại diện ký kết hợp đồng OEM.
Hoạt động điều phối và giao tiếp của nhóm dự án giữa OEM và SI
Một trong những khía cạnh thách thức hơn của các dự án với hệ thống tiêu chuẩn OEM là cách thức chúng được định vị trong nhóm hợp đồng đối với SI (xem Hình 5). Nhà tích hợp thường là nhà thầu phụ hoặc nhà cung cấp cho nhà thầu điện, tổng thầu hoặc người dùng cuối. Tuy nhiên, trong hầu hết các trường hợp, các nhà cung cấp OEM là nhà thầu phụ hoặc nhà cung cấp cho tổng thầu. Điều này có thể đưa ra một thách thức về mặt thiết lập giao tiếp giữa SI và OEM, và do đó SI phải là bên chủ động thúc đẩy thiết lập mối quan hệ này.
Hoạt động này cần phải diễn ra sớm trong dự án vì có thể mất thời gian để thiết lập các kênh liên lạc và do đó cần có phản hồi đối với các yêu cầu cung cấp thông tin. Một số nhóm hợp đồng sẽ cho phép SI và OEM giao tiếp trực tiếp để trao đổi các chi tiết kỹ thuật. Tuy nhiên, điều này không phải lúc nào cũng đúng như vậy, và các kênh giao tiếp theo hợp đồng cần được tôn trọng.
Phía SI cần phải tích cực bổ sung để đưa ra các yêu cầu rõ ràng về thông tin và thúc đẩy các hạng mục này chuyển qua một chuỗi hợp đồng gồm các bên liên quan có thể không coi những yêu cầu và phản hồi này là con đường quan trọng hiện tại. Trong mọi trường hợp, việc điều phối trở nên khó khăn nếu có những thay đổi thiết kế được xác định liên quan đến thiết bị OEM và thiết bị do SI cung cấp và định cấu hình.
Các phần thông số kỹ thuật liên quan đến phạm vi nhà cung cấp OEM thường tách biệt với các yêu cầu và tiêu chuẩn đối với SI liên quan đến việc tích hợp thiết bị của nhà cung cấp. Sự phân biệt này rất quan trọng vì thông tin mà SI cần từ OEM phức tạp hơn thông tin mà OEM cần từ SI.
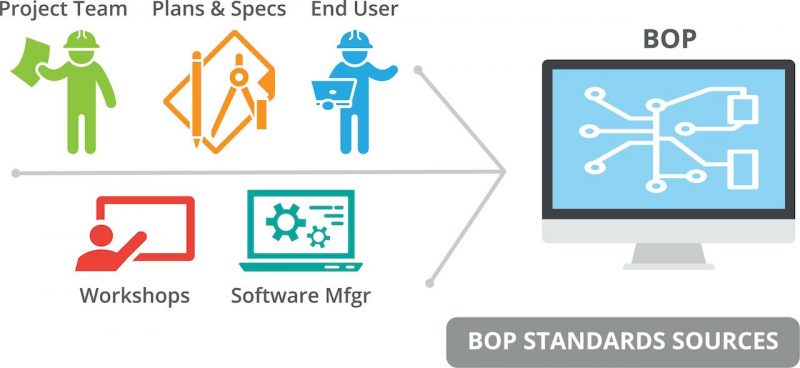
SI cần một số thông tin để hoàn thiện phạm vi kế hoạch của mình, liên quan đến việc tích hợp một số thông tin quy trình cho thiết bị OEM vào hệ thống điều khiển BOP. Điều này bao gồm nền tảng phần mềm SCADA cho BOP cũng như trao đổi dữ liệu giữa các OEM của PLC và các PLC của hệ thống điều khiển khác có mối quan hệ kiểm soát quan trọng với thiết bị OEM. SI cũng phải quy định thông tin nào được yêu cầu từ mỗi OEM để đáp ứng các kế hoạch và thông số kỹ thuật yêu cầu dữ liệu quy trình thiết bị OEM được tích hợp vào hệ thống điều khiển BOP.
Các chiến lược tích hợp để thành công
Để đáp ứng những thách thức nêu trên sử dụng sự kết hợp của các chiến lược, SI cần thực hiện lấy thông tin về nhà cung cấp OEM, xác định những thành phần nào cần tích hợp, xác định các tiêu chuẩn phần mềm phù hợp và tích hợp công nghệ giữa thiết bị OEM và BOP.
Lấy thông tin nhà cung cấp OEM
Độ thành công sẽ khác nhau tùy thuộc vào OEM và cấu trúc nhóm hợp đồng cũng như sự bền bỉ của SI. Thông tin cần thiết từ nhà cung cấp OEM có thể khác nhau, nhưng có một số mặt khác sẽ lý tưởng trong hầu hết các trường hợp. Chúng bao gồm các chương trình PLC, hoặc tối thiểu là các thẻ có sẵn để trao đổi dữ liệu với các PLC khác hoặc tích hợp với nền tảng BOP SCADA, cũng như thông tin về thiết bị OEM bao gồm các bản nộp cho nhóm hợp đồng.
Nếu có các OIT được liên kết với thiết bị OEM, các chương trình phần mềm này cũng phải được giao nhận. Các ứng dụng OIT tại chỗ có thể làm sáng tỏ các thẻ được truy cập trong OEM PLC để cung cấp trạng thái, kiểm soát và báo động. Thông tin này cũng có thể giúp giải quyết các câu hỏi về dữ liệu thích hợp được tích hợp vào ứng dụng phần mềm SCADA của BOP.
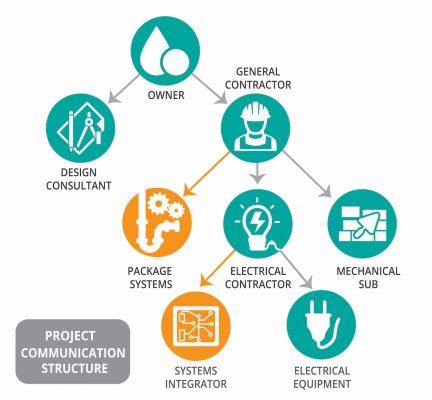
Tùy thuộc vào OEM, một số thông tin này có thể không được cung cấp lúc đầu vì nhiều OEM coi các ứng dụng phần mềm này là một phần sở hữu trí tuệ (IP) của họ. Do đó, việc có được nó có thể là một thách thức nếu các kế hoạch và thông số kỹ thuật hoặc tài liệu hợp đồng khác không chỉ rõ nhà cung cấp được yêu cầu cung cấp thông tin này. Người dùng cuối, tổng thầu và các bên khác trong nhóm hợp đồng như nhà tư vấn hoặc kỹ sư thiết kế có thể hữu ích để thuyết phục OEM cung cấp thông tin này. Trong một số trường hợp, chỉ một danh sách thẻ được cung cấp, hiển thị các biến được xác định cho tích hợp nền SCADA của BOP hoặc trao đổi dữ liệu với các PLC khác.
Danh mục các biến này cùng với các kế hoạch và thông số kỹ thuật và bất kỳ đệ trình OEM nào, đôi khi là đủ để SI thành công, nhưng điều này phải được xác định trong từng trường hợp cụ thể. Cách tiếp cận tốt nhất là phải rõ ràng và hiệu quả với các yêu cầu và cung cấp lý do đầy đủ cho lý do tại sao thông tin là quan trọng.
Sẽ rất hữu ích khi SI đáp ứng các yêu cầu OEM. Thể hiện sự lịch sự và tôn trọng bằng cách đáp lại có thể tăng cơ hội nhận lại được điều tương tự (xem Hình 6). Yêu cầu trao đổi trực tiếp với OEM luôn là điều đáng quan tâm vì nó tạo điều kiện giải quyết vấn đề nhanh hơn.
Xác định những thành phần để tích hợp
Một số yếu tố xác định thông tin nào từ thiết bị OEM cần được tích hợp vào hệ thống điều khiển BOP và việc tích hợp này phải diễn ra ở cấp độ nào. Hai lĩnh vực chính mà sự tích hợp xảy ra là ở các PLC quy trình và ở ứng dụng phần mềm SCADA BOP.
Ở cấp độ PLC, thường yêu cầu trao đổi thông tin giữa PLC của OEM và PLC của khu vực quy trình khác. Điều này liên quan đến các mối quan hệ kiểm soát giữa các thiết bị của nhà cung cấp OEM nằm ở thượng nguồn, hạ nguồn hoặc trong một quá trình đào tạo. Các biến quy trình bao gồm lưu lượng, áp suất và giá trị phân tích – cũng như, điểm đặt, khóa liên động, phép, cảnh báo và lệnh điều khiển – đều là các thành phần chung của mối quan hệ kiểm soát và do đó yêu cầu trao đổi dữ liệu với thiết bị OEM.
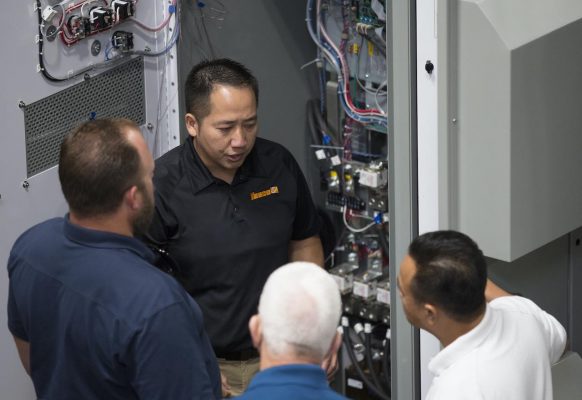
Mặc dù có những trường hợp thiết bị OEM cần thông tin từ nơi khác trong hệ thống hoặc dữ liệu quy trình OEM được yêu cầu bởi một PLC khác, hầu hết các trường hợp đều bao gồm sự kết hợp của cả hai. Lý tưởng nhất là dữ liệu được trao đổi giữa PLC của OEM và các PLC khác trong hệ thống được xác định rõ ràng trong kế hoạch và thông số kỹ thuật và chính xác. Thông thường hơn, thông tin này là gần đúng với rất ít hoặc không xem xét những gì có sẵn từ mỗi OEM PLC.
Trong những tình huống khó khăn nhất, thông tin này không được xác định rõ ràng hoặc không tồn tại, đòi hỏi sự hợp tác trong nhóm dự án để xác định những gì cần trao đổi và hậu cần cho việc phân phối. Điều quan trọng là phải thiết lập các đường dây liên lạc mở giữa nhà cung cấp và các thành viên trong nhóm hợp đồng.
Nhiều yếu tố thiết bị OEM có thể được tích hợp với nền tảng phần mềm SCADA BOP. Chúng bao gồm kiểm soát, báo động, thông tin quy trình chi tiết và dữ liệu được ghi lại lịch sử để báo cáo, xu hướng hoặc hồ sơ quy trình. Thông tin từ PLC của OEM được tích hợp vào hệ thống SCADA BOP sẽ được trình bày chi tiết trong kế hoạch và thông số kỹ thuật, cụ thể là sơ đồ đường ống và thiết bị (P & ID) và xác định từng biến quy trình được yêu cầu ở cấp SCADA.
Thông tin này không phải lúc nào cũng đầy đủ chi tiết. Điều này có thể xảy ra vì nhiều lý do, chủ yếu là do thông tin được tích hợp rất rộng và được trình bày chi tiết ở những nơi khác trong tài liệu đặc tả. Điều này đòi hỏi nhiều phân tích hơn để xác định danh sách thẻ SCADA cho mỗi gói OEM.
Với một số loại thiết bị quy trình của nhà cung cấp OEM, chẳng hạn như hệ thống tia cực tím được sử dụng làm công nghệ khử trùng, có quá nhiều biến được đọc vào hệ thống SCADA BOP. Điều này xảy ra khi quy trình của OEM có nhiều biến số cần theo dõi và các kế hoạch và thông số kỹ thuật yêu cầu thông tin này có sẵn trong hệ thống SCADA BOP. Điều này có thể ảnh hưởng đến các mô hình cấp phép nền tảng SCADA được gắn với số lượng thẻ, vì vậy cần xem xét ở đây để xác định tác động tổng thể.
Một mục khác thường yêu cầu một số cuộc điều tra là các điều khiển của người vận hành đối với thiết bị OEM như các điểm đặt và chức năng điều khiển bằng tay. Điều này thường được thiết lập để tồn tại cục bộ thông qua OIT và không nhằm mục đích thực thi từ một nguồn từ xa khác như hệ thống SCADA BOP. Màn hình cấu hình OEM có xu hướng cung cấp quá nhiều quyền kiểm soát hoặc lượng khả năng cấu hình không phù hợp nếu được tích hợp ở cấp ứng dụng SCADA. Việc xác định những gì nên và không nên kết hợp vào hệ thống SCADA BOP nên được thảo luận với OEM và các bên liên quan của nhóm hợp đồng.
Báo động là một lĩnh vực khác cần được đảm bảo. Một số thiết bị OEM có một số lượng lớn các cảnh báo cụ thể cục bộ nhưng chỉ cung cấp các cảnh báo chung hợp nhất để tích hợp ở cấp SCADA BOP. Khi hệ thống SCADA là giao diện chính cho nhân viên vận hành, điều này có thể cung cấp ít thông tin đầy đủ hơn, yêu cầu phản hồi của người vận hành cục bộ tại giao diện OEM để hiểu trạng thái của thiết bị OEM hoặc cảnh báo quy trình.
Một thách thức đáng báo động đáng báo động là việc đồng bộ hóa các trạng thái báo nhận giữa hệ thống SCADA BOP và OEM OIT cục bộ, điều này hiếm khi có thể đạt được nếu không có các phương pháp không chính thống như sử dụng phương pháp “man-in-the-middle” để cấp phát thanh ghi PLC để giữ trạng thái báo nhận cho cả hai hệ thống .
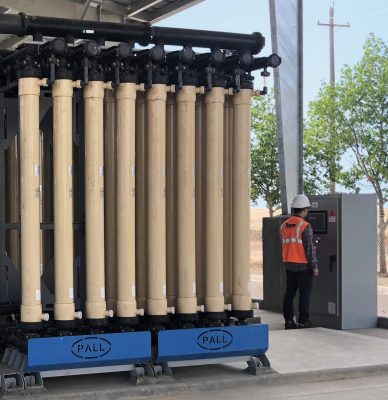
Nhân viên vận hành thường cần xác nhận các cảnh báo tại SCADA BOP và tại OIT cục bộ để đồng bộ hóa các trạng thái cảnh báo. Hơn nữa, các cuộc thảo luận về chiến lược báo động có thể dẫn đến yêu cầu tích hợp tất cả các cảnh báo, điều này cũng có thể ảnh hưởng đến giấy phép SCADA BOP gắn với số lượng thẻ.
Việc xác định thông tin nào sẽ được tích hợp ở giai đoạn đầu của một dự án là rất quan trọng để định cỡ hệ thống SCADA BOP và phát triển kế hoạch phần mềm kỹ thuật. Như trong trường hợp trao đổi dữ liệu PLC, cần phân tích để đảm bảo thông tin cần thiết được tích hợp là rõ ràng, chính xác và phù hợp.
Xác định sự liên kết của các tiêu chuẩn phần mềm
Có một số lĩnh vực mà tiêu chuẩn phần mềm OEM có thể không phù hợp với hệ thống điều khiển BOP, bao gồm màu sắc, ký hiệu đồ họa, phương pháp điều khiển, báo động, xu hướng, điều hướng, cấu trúc ứng dụng đồ họa tổng thể và phương pháp mã hóa PLC. Ví dụ: nếu có sự khác biệt về tiêu chuẩn màu giữa giao diện OEM OIT và hệ thống SCADA, cần có quyết định để xác định cách thông tin này được hiển thị tại hệ thống SCADA, giả sử OEM sẽ không thay đổi bảng màu của họ. Nhiều phương pháp có thể tiến hành trong trường hợp này, với việc lựa chọn phương pháp tốt nhất phụ thuộc vào những gì được xác định là các yếu tố quan trọng nhất.
Môi trường hội thảo thường là một diễn đàn thành công để tìm ra các chi tiết của tiêu chuẩn phần mềm SCADA và các thành phần thiết kế khác liên quan đến việc tích hợp thiết bị OEM. Thông qua quá trình hội thảo hoặc sự hợp tác khác trong nhóm hợp đồng, có thể xác định rằng điều quan trọng nhất là màu sắc phải phù hợp. Điều này có thể dẫn đến sự sai lệch trên hệ thống SCADA cho khu vực quy trình OEM cụ thể này để khớp với màn hình cục bộ. Cũng có thể xác định rằng điều quan trọng hơn là tiêu chuẩn hệ thống SCADA phải được duy trì nguyên vẹn trong suốt ứng dụng SCADA chính và do đó, các màn hình OEM sẽ cần được sửa đổi để phù hợp với tiêu chuẩn phần mềm hệ thống tổng thể (xem Hình 7).
Sẽ có nhiều cuộc thảo luận cần thiết để phát triển một cách tiếp cận cho từng lĩnh vực khác nhau. Không có câu trả lời đúng hay sai trong vấn đề này, vì các quyết định liên quan nhiều hơn đến nhu cầu của người dùng cuối và mục đích của thiết kế. Kết quả là, cuối cùng họ phải dựa vào ý kiến đóng góp của các thành viên khác nhau trong nhóm hợp đồng. Tất cả các quyết định phải được lập thành văn bản để tất cả các bên hiểu những gì đang được chuyển giao như một sản phẩm cuối cùng.
Tích hợp công nghệ giữa thiết bị OEM và BOP. Khi xác định rằng việc trao đổi dữ liệu là cần thiết giữa PLC của OEM và PLC của nhà máy khác hoặc phần mềm SCADA BOP, bước tiếp theo là xác nhận xem có các phương pháp cho phép các thành phần này giao tiếp với nhau hay không. Điều này liên quan đến việc xem xét kỹ hơn kiến trúc mạng, phương tiện, thiết bị, giao thức và trình điều khiển I/O được sử dụng để thu thập dữ liệu cho nền tảng phần mềm SCADA.
Nếu thiết kế thiếu các điều khoản cần thiết, cần có các bộ phận bổ sung để tạo điều kiện giao tiếp giữa các thiết bị khác nhau. Đây có thể là các thành phần mạng, mô-đun giao tiếp PLC, thiết bị dịch giao thức hoặc cổng hoặc thành phần phần mềm – một số hoặc tất cả có thể cần thiết để phần mềm SCADA BOP có thể truy cập dữ liệu quy trình quan trọng. Phân tích kỹ lưỡng có lợi cho việc giúp tránh các vấn đề trong giai đoạn sau của dự án mà thời hạn có thể bị bỏ lỡ hoặc nơi không có trao đổi dữ liệu quan trọng cho các hoạt động khởi động và vận hành.
Cũng như nhiều khía cạnh khác của tích hợp OEM, nguyên tắc “càng sớm càng tốt” thể hiện ý tưởng chung khi xác định các vấn đề tiềm ẩn và phát triển các giải pháp.
Khuynh hướng phát triển dự án với SI và OEM
Tích hợp thiết bị OEM tạo ra những thách thức riêng cho SI chịu trách nhiệm kết hợp các hệ thống đặc thù này vào hệ thống kiểm soát BOP tổng thể. Phân tích thiết kế ban đầu và tập trung vào các vấn đề liên quan đến tích hợp thiết bị OEM là cần thiết để phát triển một sản phẩm tổng thể phù hợp với mục đích của thiết kế hệ thống kiểm soát quá trình và đáp ứng nhu cầu của các bên liên quan của dự án và người dùng cuối. Giao tiếp là một thành phần quan trọng để tích hợp và liên kết thành công, bao gồm tổng hợp và linh hoạt các quyết định hợp tác mà nhóm hợp đồng đưa ra trong suốt quá trình phát triển của dự án.
Giới thiệu về CTI SUPPLY
CTI SUPPLY với đội ngũ kỹ sư hơn 10 năm kinh nghiệm cung cấp các hệ thống điều khiển chất lượng cao và đáng tin cậy. CTI SUPPLY là nhà tích hợp hệ thống điều khiển trong ngành tự động hóa. Các dịch vụ hệ thống điều khiển của CTI SUPPLY bao gồm thiết kế bảng điều khiển tùy chỉnh, xây dựng và vận hành, lập trình PLC và HMI, tích hợp hệ thống robot, quản lý hệ thống, thiết kế hệ thống SCADA và phần mềm giám sát máy móc.
Các dịch vụ cung ứng giải pháp tự động hóa của CTI SUPPLY
- Hệ thống điều khiển PLC & tủ bảng điện điều khiển
- Hệ thống PLC, SCADA giám sát, điều khiển sản xuất công nghiệp
- Hệ thống PLC, SCADA giám sát, điều khiển hệ thống sản xuất thực phẩm, cấp nước, xử lý nước thải, xi măng, phân bón, dệt may,..
- Hệ thống điện động lực
Với kinh nghiệm dày dặn trong đa dạng loại hình hệ thống điều khiển tự động hóa từ nhiều nền tảng như Siemens, Rockwell Automation, Wonderware, Beckhoff, Schneider Electric, Omron, Yokogawa,…, CTI SUPPLY tích hợp và cung cấp giải pháp trọn gói về lộ trình cung ứng dịch vụ lập trình hệ thống PLC SCADA của nhà máy thông qua quá trình khảo sát, phân tích, trao đổi làm việc trực tiếp với OEM và hoạch định kế hoạch chi tiết cho khách hàng.
Tìm hiểu thêm về dịch vụ cung cấp giải pháp tự động hóa – lập trình PLC SCADA HMI của CTI SUPPLY.
Liên hệ với CTI SUPPLY qua mail: sales@ctisupply.vn. Hoặc hotline (+84) 906 494 486 để được hỗ trợ giải pháp và báo giá dự án nhanh nhất.