Basically, virtual commissioning is the practice of using “virtual” simulation technology to “commission”—design, install or test—control software with a virtual machine model before you connect it to the real system.
Contents
Using the TIA Portal to simulate, validate, and optimize controllers and machines
Machine development is usually sequential: Mechanical design, electrical design, and automation are performed one after the other. If a mistake is made anywhere in the development process and isn’t detected, the error costs grow by a factor of ten per phase of development. Undetected errors can cause expensive damage during commissioning. If the machine is in operation and requires optimizing or modernizing, the ideal moment for downtime has to be found – naturally, the operator wants to keep downtimes to a minimum.
The alternative is to virtually commission a machine in the TIA Portal. Based on a digital twin of the new machine, the mechanical design, electrical design, and automation engineering can be performed in parallel. Simulations and tests uncover faults at an early stage, with the result that real commissioning on site at the customer’s is performed faster and with less risk. This enables you to reduce the time to market, lower costs, and increase flexibility and productivity. Commissioning a machine at a customer’s facility is the decisive moment: Are extensive corrections needed, or does everything go as planned? To reduce the risk and effort associated with the actual commissioning, virtually commissioning the machine using PLCSIM Advanced in the TIA Portal offers an efficient alternative. This approach even makes it possible to simulate and optimize the interaction between individual components of entire production lines in a virtual environment.
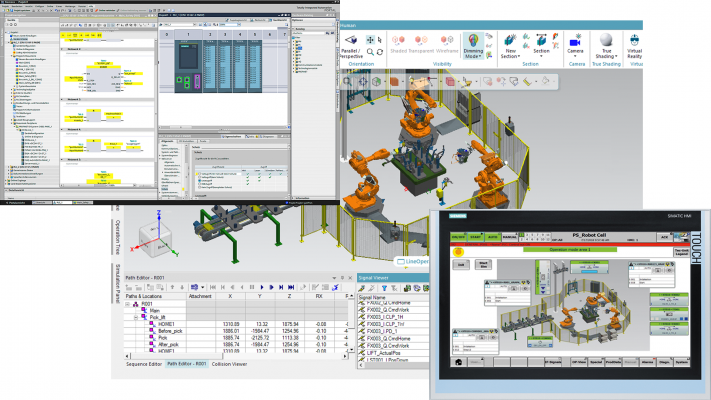
Simulation and virtual commissioning with TIA Portal
Faults are inevitable during the development of a machine or plant. However, they can cause high costs and enormous effort when they are only detected during real commissioning. Integration in a line or plant involves risks as well. A solution is simulation with TIA Portal. Based on the digital twin of a new machine or line you’re able to parallelize engineering, test functions and detect faults earlier, simulate the interplay of the machine in a line, and optimize operation while its running. Also, additional services can be offered based on the digital twin of the machine, which can also be used for marketing, i.e. at fairs or in a virtual showroom.
Reduce time and risk in machine building and plant engineering and lay the foundation for new business models
Virtual commissioning your automation systems prior to launch
Tecnomatix virtual commissioning solutions let you debug automation control logic and PLC code in a virtual environment before download to real equipment. By simulating and validating your automation equipment virtually you can confirm that they will work as expected and significantly reduce system installation cost and startup time.
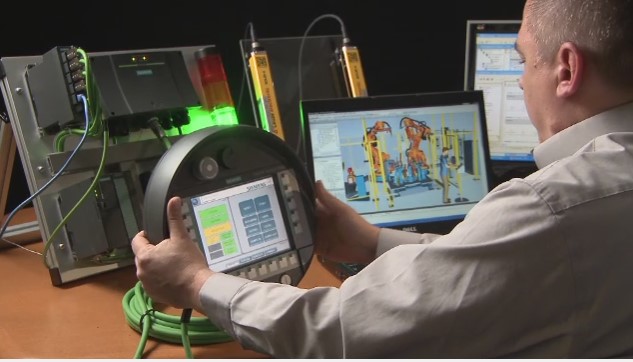
How it Works
You’re likely familiar with traditional commissioning but, just in case, let’s explore this from the ground up. The difference between real physical commissioning and virtual commissioning is that a real commissioning process involves testing directly on a real manufacturing system (i.e. a machine), a real controller (i.e. PLC), and other necessary devices, including sensors and actuators. Virtual commissioning, however, uses virtual replicas of the system’s components and has several configuration options.
Virtual commissioning of a machine’s dynamics combines three important pieces: a digital model (sometimes referred to as a digital twin), the controller code that governs the motion and responds to sensor feedback, and a development environment that allows the two to run together.
For this to be practical for the manufacturing and automation industries, virtual models need to be sufficient for their usage outside of niche experts. The development of advanced, model-driven design practices has taken form in a digital twin. Besides the digital twin, the software standards for model connectivity have also seen drastic improvements. Together, these technologies are permitting the widespread practicality of virtual commissioning throughout the automation industry.
With the right tools in place, organizations can adopt virtual commissioning techniques for their machine design projects. They may use these techniques in order to reduce their overall commissioning time, to reduce commissioning costs, or to create a more reliable time to market for reputation purposes. While the applications and specifics can vary, a typical virtual commissioning process has many commonalities.
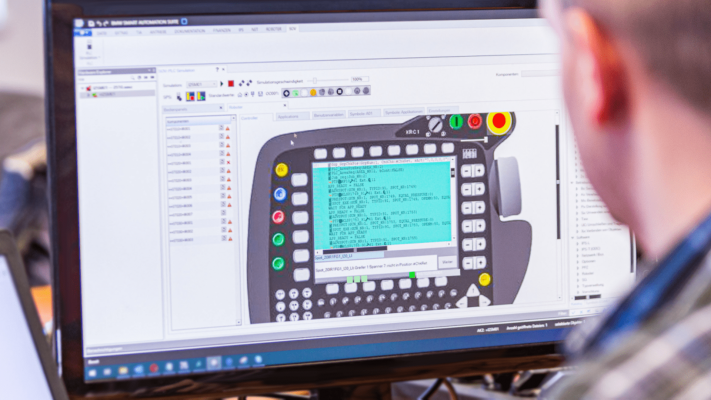
The Benefits of Virtual Commissioning
One major advantage is that it brings forward the commissioning phase. By using virtual prototypes, manufacturers can test control software in parallel with other engineering phases (Reinhart and Wünsch,. 2007). This vastly reduces the risks of errors later in the development process.
Virtual commissioning also allows testing to be performed in a virtual environment. This commissioning approach allows for improved software quality and increased safety for workers. It also reduces the risk of damaging machinery if tests are carried out in real-time. And that’s just the start – commissioning with a digital twin brings so many more benefits to the table.
Thinking Forward
In the manufacturing and automation industries, adopting new development techniques has become a key requirement for success. As demands on product requirements increase, design risks pose significant problems, threatening the success of those trying to keep pace. The technique of virtual commissioning promises to reduce the significant delays and costs associated with system integration and commissioning. While previously only possible by niche experts, powerful modeling tools and compatible information standards have paved the way for modern, accessible virtual commissioning solutions. This technology is heavily invested in by companies and research groups around the world, creating powerful techniques for model-based design. As these technologies develop, their role in the automation industry will continue to grow into an essential component of product design. Curious about how to get started with Virtual Commissioning? Read more here.
CTI SUPPLY – Automation System Integrator
We provide offshore-designing and programming services for automation systems. CTI SUPPLY has years of experience implementing industrial automation solutions utilizing PLCs. We are capable of developing new PLC systems from the ground up and also troubleshoot, update, maintain and add up to pre-existing PLC systems. Our engineers have hands-on experience in working in multinational corporations, high-tech automated manufacturing plants and the oil and gas industry.
- ALLEN BRADLEY/ROCKWELL AUTOMATION
- SIEMENS
- MITSUBISHI
- SCHNEIDER ELECTRIC
- BECKHOFF
- OMRON
Are you looking for a vendor with lower expense and better service? Contact us.