The maintenance of rolling machine is very important, good maintenance can effectively extend the using life. Customers should pay attention to the plate rolling machine maintenance. Generally, the rolling machine working efficiency and failure rate are closely related to operators. As operators of dangerous equipment, they should know more about relevant knowledge to effectively avoid disoperation or incidents. Next, let’s learn about how to maintain rolling machines in daily production.
Contents
The cleaning operation of the plate rolling machine
Before cleaning the steel plate rolling machine, it is necessary to install a filter device or a filter on the pipeline for cleaning the oil. The automatic plate rolling machine should be heated, and the temperature of the hydraulic oil is generally 50-80 ℃. When cleaning, you can knock the attachments in the oil pipeline with non-metallic materials. In addition, the right hydraulic oil must be used, and other liquids such as motor’s oil and automobile oil should not be used to prevent the erosion of the hydraulic system.
The plate rolling machine maintenance
Routine rolling machine maintenance
The daily maintenance of steel plate rolling machine is very important. Only in this way can the service life be prolonged.
1. Check whether the external structural parts of the sheet metal rolling machine are damaged, deformed, etc.
2. Check whether the operation console and operation switches, limit positions, and indicator lights are normal.
3. Check the pipeline system for leaks.
4. Check the oil pump, solenoid valve, and oil cylinder for oil leakage.
5. Check whether there is any abnormality in the operation of the upper and lower rollers and the wear of the sliding bearings.
6. Check whether the pressure gauge is normal.
7. Check whether there is any abnormal noise when the motor is running.
8. Check and lubricate parts:
- Reducer
- Main drive open-gear
- Upper roller lifting guide
- Sliding bearings at both ends of the upper and lower rollers.
9. The above maintenance items shall be borne by the operator.
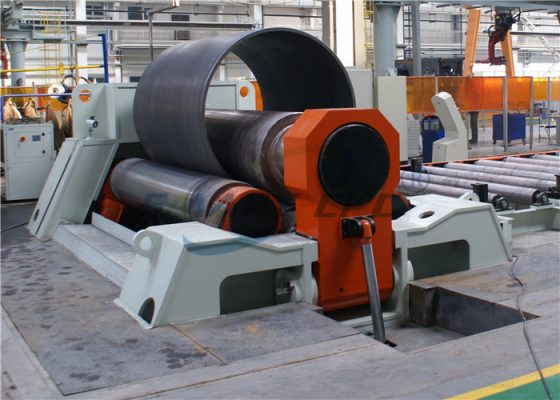
Remarks
- Lubricate the machine according to the lubrication diagram.
- Strictly follow the operation manual of the bending process to ensure safe operation of the equipment
- In the operation of the machine, the operators should coordinate with each other, remember without authorization, it is prohibited to start the machine.
- Operators must pay great attention to safety when using the plate rolling machine, to prevent the hand from being pressed by the steel plate and contacted with the steel plate.
First-level technical maintenance
The following work add-ons:
1. Check whether the routes and accessories of the electrical system are intact.
2. Check whether the oil level in the hydraulic system oil tank is normal, and refill in time.
3. Check the operation of the hydraulic system, and check the performance status of the machine under high load.
4. Check the clearance of the lower bearing of the body of the plate rolling machine and the clearance of the sliding guide of the frame.
5. Check the open gear meshing.
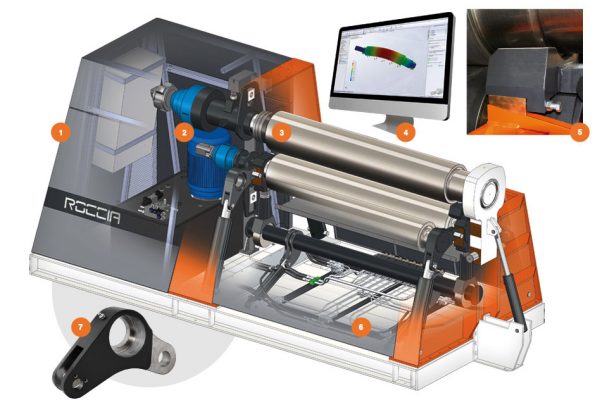
Secondary technical maintenance – hydraulic system maintenance
1. Change the hydraulic oil every one to two years.
2. Empty the hydraulic oil in the crude oil tank when changing oil, check for gunk and metal chips at the bottom of the oil tank, and clean the oil tank.
3. When checking oil, the filter should be replaced or thoroughly cleaned.
4. The hydraulic control elements (valves) are cleaned as appropriate.
Components of plate rolling machine maintenance
1. External maintenance parts
- Clean the outer surface of the machine and keep it clean.
- Match the missing parts.
2. Lubricated parts
Check the oil filling holes, clean, add lubricating oil as appropriate.
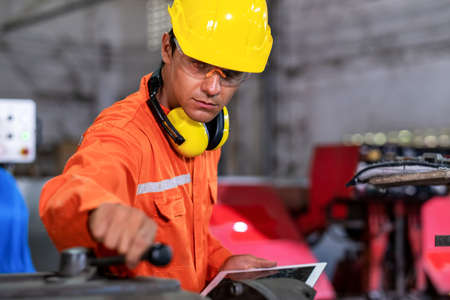
3. Electrical parts
- Wipe the electrical box to clean dust and grease.
- Check the circuit is in good condition, the hose protection connection is reliable, and the performance is good.
- Check the safety shield.
- Clean the motor, check the bearings, and replace the grease.
- Repair or replace carbon brushes and other components.
4. Roller parts
- Check and adjust the accuracy of the roller to make it achieve smooth movement.
- Repair or replace damaged parts.
To sum up, the customers who adhere to do a good job in the daily maintenance, can extend the service life of components and prolong the wear cycle of mechanical parts. It can prevent the occurrence of the accident malignant accident to ensure the long time stable work. Furthermore, it also give full use of rolling machine advantages to achieve the best technical performance.
CTI SUPPLY – MAINTENANCE TECHNICAL SUPPORT
CTI SUPPLY maintenance engineers at the on-site manufacturing plant ready to handle and resolve technical issues of industrial production lines. In particular, the unit provides a variety of maintenance and repair services as followings:
- Electrical automation system applied with PLC/SCADA/HMI Foundation
- Food processing and packaging system
- Semi-Automatic to Fully Automatic equipment
- Multiple Hydraulic and pneumatic systems
- Automatic conveyor system
- Pressing, Fine Blanking, Rolling, Cutting, Bending Machine
- Hardening and Tempering Furnace system
CTI SUPPLY improves the profitability for clients by performing different scope of installation, commissioning and maintenance services under OEM’s instruction at the customer’s site. The scope of activities is diverse, our team experienced with many years of designing, programming and maintaining machinery in the oil and gas industry and large European manufacturing plants in Vietnam. In particular, we plays the role as local technical support on site for customers under OEM authorization with in-time flexibility and activeness.
Are you looking for a rolling machine maintenance team? Contact us.