AI can play a vital role in optimizing power and water consumption, which creates immediate benefits for environment, operating costs and margins. For instance, fresh products like fruit and vegetables can vary dramatically in size, shape, color or texture, adding a layer of complexity to the production line. AI solutions can easily recognize variances, removing contaminants without wasting whole batches and continually adjusting water and energy usage according to requirements.
From reactive to preventive to predictive to prescriptive, maintenance in food and beverage processing plants has come a long way. Food and beverage processing ranges from receiving materials to production, quality assurance and inspection, and the packing and dispatching of final goods.
All of this occurs in a very specific environment (harsh, humid, hot or cold, for instance), which requires continuous maintenance of equipment, storage and workspaces, according to Tatjana Milenovic, global head of food and beverage industry segment at ABB Inc., an industrial automation company. “Food safety and sustainable operations with minimal downtimes are the highest priorities,” she says.
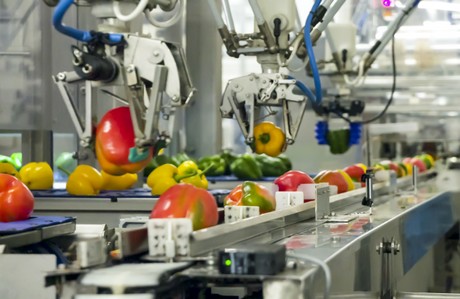
Big data and deep learning make artificial intelligence useful to understanding data, making predictions and suggesting recommended actions without explicit human instructions. There are three areas to consider with AI: process optimization, predictive maintenance and production efficiency, says Massimo Bonardi, technical and managing director/co-founder, Antares Vision, a solutions provider in inspection systems, track and trace, and smart data management.
The benefits are far-reaching, including shortened time to market, streamlined machine reconfiguration and reduced mechanical complexity—including reduced production and maintenance costs. Preventive maintenance is driven by metrics monitoring to avoid downtime that otherwise may have been unforeseen. Elements include everything from production line sensors and quality inspection controls to smart connections with electronic recordkeeping and manufacturing execution systems (MES).
Contents
Reducing maintenance downtime with AI
When it comes to maintenance in processing plants, having the data and knowing how to use it is the key to system upkeep. Failure is managed before it happens, by monitoring correlated data to find patterns and repeatability. “It’s an information cause-and-effect analysis, performed in near real time,” Bonardi says. “The better the maintenance predictivity, the more downtime can be reduced to benefit both output optimization and production schedules. A crucial factor is determining the ‘real-time’ condition of equipment rather than guesstimating based on average, per-machine maintenance expectancy,” he says.
Traditionally, maintenance was done by reactively acting as equipment malfunctioned.
“Preventive maintenance was applied to maintain and replace parts before they failed, independently from their actual condition,” Milenovic says. “The development of the digital concept of predictive and condition-based maintenance allows food processors to plan maintenance more efficiently, reducing downtime due to broken parts and eliminating maintenance work which is not presently needed.”
Often residing in different systems, maintenance data typically is fragmented and non-interoperable. “With the emerging trend toward data being aggregated in centralized asset management databases and enterprise resource planning (ERP) systems, available maintenance data is able to be leveraged in AI-enabled activities like perceiving the surrounding environment, applying reasoning to the data context and making optimal maintenance decisions,” Milenovic says.
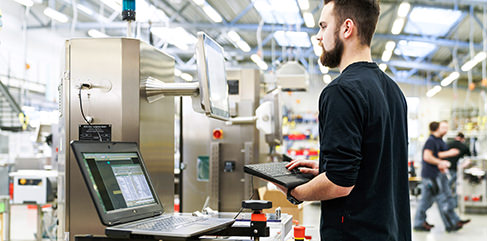
WIPOTEC-OCS offers an enhanced washdown system for its SC-WD-6000-B X-ray scanner. Capable of inspecting many tons of bulk meat per hour and offering foreign body detection sensitivity, the scanner is equipped with an HD-TDI camera detector. In conjunction with the metal-ceramic tube, it generates extremely high-resolution X-Ray images for the unit’s custom-designed image processing software.
Jim Renehan, senior marketing manager for WIPOTEC-OCS, a manufacturer and supplier of in-motion weighing and X-ray scanning equipment, says, “We are seeing a high degree of automation, that sometimes incorporates modular plant construction, but it is very rare that we see holistic concepts in the sense of smart food and beverage processing plants. There seems to be a fair amount of skepticism on the plant floor when it comes to AI. However, the food processors that we work with in general are standardizing their processes via ERP and MES.”
The use of AI in the Maintenance
While predictive maintenance uses sensors to precisely collect data regarding equipment condition and overall operational state to predict when a failure will occur, the use of AI in the maintenance domain elevates the function to that of prescriptive maintenance, Milenovic says. “Failures are not only anticipated, but actions are also recommended. The potential outcomes of the recommended actions are then processed and projected.” For example, a sensor-based predictive concept for a motor or bearing will indicate when the equipment is likely to fail given its temperature and vibration profile. “The prescriptive method will indicate the relation and impact between motor temperature and speed, and suggest, for example, to reduce speed by 10% to achieve 30% more working hours before the equipment is likely to stop,” she says.
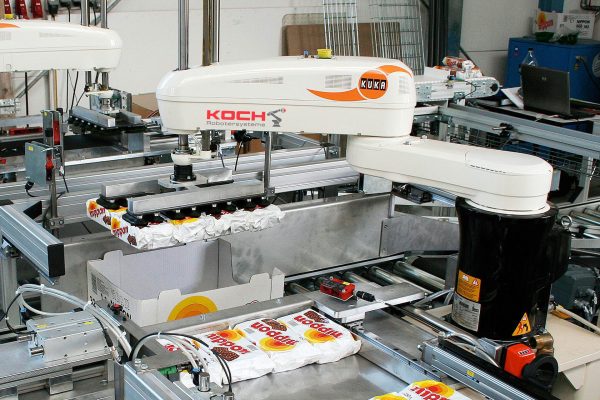
Prateek Joshi, CEO at Plutoshift, a performance monitoring platform provider, adds that because food and beverage processors are increasingly digitizing their operations, that allows them to collect operational data and store it in an organized way. “But this data is not being used to get their work done,” he says. “The operators still rely on manual workflows (e.g. spreadsheets) to do work, which means they are working in a reactive way as opposed to a proactive way. AI can be leveraged to automate these workflows and transform to a more proactive way of working,” he says. “The positive trend within this market segment is that the C-suite leaders are showing strong commitment toward data intelligence and automation.”
Advantages in using AI in Food Processing Equipment Maintenance
Bonardi says AI is integrated with the Antares Vision line performance monitoring system, and maintenance represents a key value in production process, able to make a difference in efficiency challenges and KPIs. “Just to make an easy example, if after 10,000 rpm we need to change the conveyor belt in a production line, the line is going to be stopped, there will be a cost related to downtime, to the production stop, to the spare parts replacement,” he says. “But it’s instead key to be able to predict any breakup, collecting data and training via neural networks to monitor the relevant parameters, when some of them, for example temperature and vibration, become crucial. For this reason, we gather different kinds of data—from production line sensors, quality inspection controls, in connection with ERP and MES.”
According to Milenovic, the application of sensors for monitoring various equipment parts (motors, bearings, pumps, etc.) is a first step toward predictive maintenance. “For example, ABB smart sensors monitor temperature, vibrations and other parameters of a motor, sending alerts to initiate timely maintenance action before any downtime occurs,” she says.
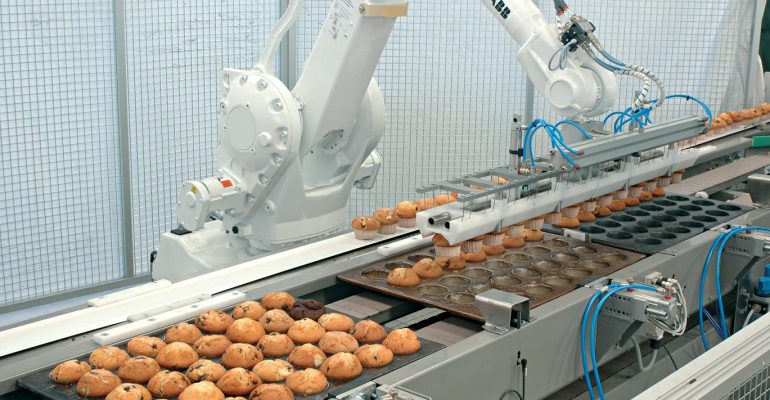
AI powered sound monitoring to detect and predict equipment failures is gaining traction in food processing plants too. “‘Listening to machines’ is utilized to monitor equipment operations and react quickly in the case of a detected problem, helping to classify the problem and initiate timely action to prevent unplanned downtime. It is a good practice not only on standard processing lines, but also with dangerous equipment to prevent employees from having to stop or directly access the processing line,” Milenovic adds.
She says that one can look at “listening to machines” as a first line of defense for maintenance, as it can detect failures earlier than other technology. “The combination of sophisticated AI and cameras has applications in the area of worker safety (e.g., ensuring required safety gear is used by operators),” she says.
Bonardi says to switch from preventive to predictive maintenance empowered with AI, first connect with data management software. “AVionics landscape allows gathering data from different equipment and to integrate with existing data source (such as ERP, MES),” he says. Then look at IIoT in production lines, including temperature, cameras, vibrations, readers, microphone or integration with existing sensors. Empowerment by AI includes data experience collection for training the neural networks and to find the patterns and correlations between relevant parameters. The final step is service for continuous updating of the neural network.
He adds that the four main reasons to switch from preventive to predictive maintenance with AI include monitoring KPIs; more accurate time to maintenance; cost saving in spare parts and equipment maintenance based on statistics; and integrating with other systems, like ERP software, to get a full picture of performance.
Challenges for AI in Maintenance
“The most common challenge of artificial intelligence is taking full advantage of its power,” says Bonardi. “The impressive amount of available data needs to be understood, managed and translated into improvements in automation to release the humans from complex jobs and mistakes, or to help them make better decisions. The combined effect of automatic learning from data, images, examples, texts, etc., together with sophisticated learning models and the high computing capacity, has yielded tremendous opportunities for progress.”
“The combined effect of automatic learning from data, images, examples, texts, etc., together with sophisticated learning models and the high computing capacity, has yielded tremendous opportunities for progress.”
Bonardi says an important element to consider is that the AI tools are fed by experience provided through examples. That means their performance is tied to how representative the dataset used to train them is. Therefore, even though AI is enabling previously inaccessible applications, AI-based systems require constant monitoring and frequent updates, in order to support the changing nature of real-world processes.
He identifies two important gaps related to the use of AI for mission critical applications:
- The need for technologies that enable new business processes supporting the collection of in-process knowledge (data refinement) and the deployment of large-scale neural networks on-premises.
- The absence of adequate tools to monitor the performance of deep neural networks in production; in the face of unexpected or unrepresented inputs in the training dataset, the current AI systems are not equipped to “stop” or provide a direct estimate of the reliability of their predictions.
Renehan says that big data and plant floor acceptance of AI are the two biggest challenges.
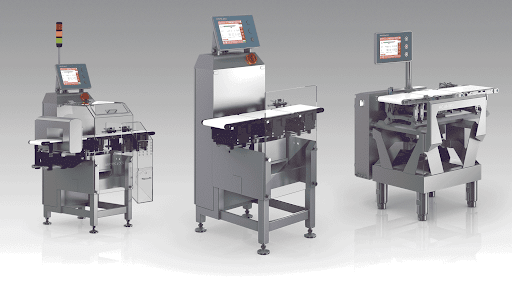
Capable of handling up to 250 products per minute, the HC-M-WD-MDi checkweigher uses WIPOTEC-OCS’s electromagnetic force restoration (EMFR) technology and has an intuitive software interface. It meets all food processing industry requirements, including IFS-compliant product control and other HACCP or LMHV/FDA hygiene regulations.
“With big data automated and tool-assisted acquisition, evaluation and analysis of manufacturing data is a must for the food processor wishing to implement Industry 4.0 and AI. However, checkweighers and X-ray scanners generate a massive amount of useful data given the production rates of today’s food and beverage processors. The food processor needs to have the network hardware and software solution that is just right for their unique situation,” he says. “The acceptance of AI at the plant floor level can only come about with a concentrated effort on the part of the food processors to adequately train their staff. Also the AI implementation needs to make sense to the workers.”
When it comes to the challenges for facilities that use predictive maintenance, Renehan says the biggest challenge to predictive maintenance is to effectively use the process data that today’s factory floor machines, such as checkweighers and X-ray scanners, provide. “Oftentimes, we see these machines being underutilized due to infrastructure limitations within the processing facility,” he says.
Bonardi says that unifying and managing massive amounts of data is the key to powering the next generation of e-commerce, tracking, fraud detection, supply chain and logistics applications.
“Complex architecture like in the food and beverage sector are difficult to run, including machinery, production lines, government compliance, suppliers (brand owners, private label manufacturers, repackagers, etc.), warehouse, wholesale distributors and logistics. A primary need is a software ecosystem designed to manage the massive data storage and the information flow.”
For this reason, he says it is essential to ensure the maximum data safety, the flexibility in different communication requirements, the minimum downtime for software updating and patch releases, and a unique point of connection to enable interface with different players, software and hardware solutions.