Water supply involves a number of components such as the water source, treatment plant, service reservoirs and the distribution system. Water utilities are responsible for the operation and maintenance of water treatment plants and distribution networks, crucial for ensuring reliability and quality of supply. This study session begins by concentrating on how adequate operation and maintenance of the water treatment and supply system can be undertaken through proper planning and maintenance implementation.
Operation and maintenance of a water supply system refers to all the activities needed to run the system continuously to provide the necessary service. The two words are very frequently used together and the abbreviation ‘O&M’ is widely used. The overall aim of operation and maintenance is to ensure an efficient, effective and sustainable system. Efficient water supply system means being able to accomplish something with the least waste of time, effort and resources; effectiveness means being successful in producing the intended result; and sustainability means able to be maintained at the best level over time – in this case, the supply of water.
Contents
Referable Checklist For Water Treatment & Supply System in Operation and Maintenance Manual
Map of all source/intakes and raw water transmission lines to plant(s)
- Map of current finished water distribution system
- Inventory List of property, service lines, equipment, tools and instruments; include manufacturer, model, serial number, and condition
- Locations of spare parts (including pumps and backup power source) and vendor contact information or repair service used
- O&M technical manuals for equipment and water system facilities (e.g. treatment plant, distribution system)
- Lists of daily, weekly, monthly, quarterly, and/or annual maintenance tasks to be performed. Log sheets for recording maintenance performed
- Location of first-aid instructions and supplies
- Contact names, telephone/fax numbers and email addresses for System operators, including contract support; Experienced operators at nearby systems who can serve as backup or provide help in an emergency
- Monitoring Plan: Current Year monitoring requirements, location of sampling or monitoring sites, sampling/reporting forms, and instructions for reporting and recordkeeping
- Location of sampling and monitoring records
- Locations of spare sample bottles, sampling technique information; monitoring plans
- Location of public notice forms and instructions
- Instructions for pressure loss in system (flow chart)
- Instructions for flushing and shock chlorinating tanks, wells, distribution system mains, etc.
- Location of secured instructions for maintaining security in your system
- Take-Away Emergency Response Plan: Flow charts for operators to handle specific problems (main breaks, chlorine leaks, chemical spills)
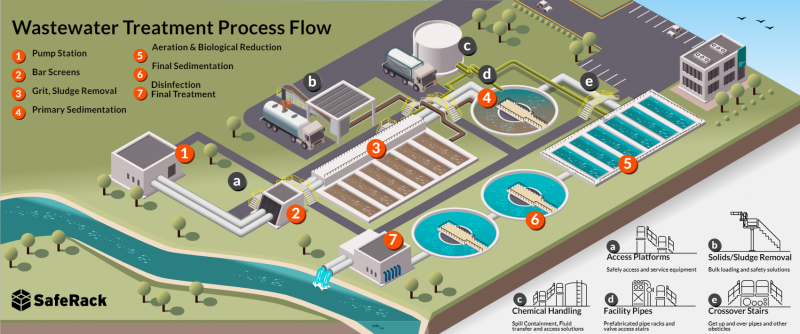
Operation & Maintenance Tasks
The need to keep this asset under control, an asset of increasing technical complexity, combined with the desire for ever greater reliability, have now rendered maintenance a strategic activity if we are to maintain. Listed below are examples of tasks that might be included in your Operations and Maintenance Manual and instructions to persons involved in servicing your water supply system. Use these lists only as examples for creating your own lists appropriate to your system.
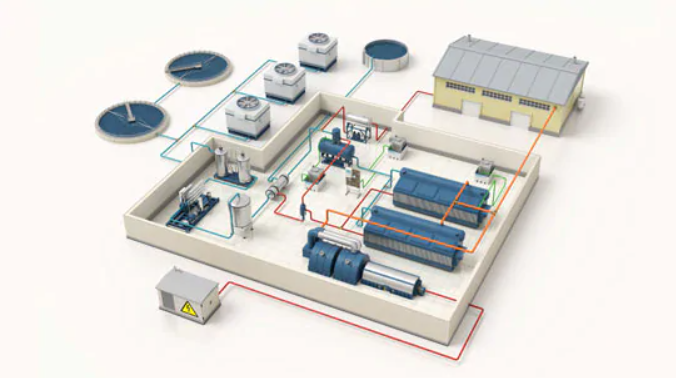
Daily Tasks
- Check water meter readings and record water production.
- Check chemical solution tanks and record amounts used.
- Check and record water levels in storage tanks.
- Inspect chemical feed pumps.
- Check and record chlorine residual at the point of application.
- Check and record chlorine residual in the distribution system.
- Inspect booster pump stations.
- Check and record fluoride concentration in the distribution system.
- Record well pump running times and pump cycle starts.
- Check instrumentation for proper signal input/output.
- Investigate customer complaints. Record threats or suspicious activity.
- Complete a daily security check.
- Inspect heater operation during winter months.
- Inspect well pumps, motors, and controls.
Weekly Tasks
- Inspect chlorine and fluoride testing equipment.
- Clean pump house and grounds. Make sure fire hydrants (if any) are accessible.
- Record pumping rate for each well or source water pump.
- Conduct weekly security check.
Monthly Tasks
- Read electric meter at pump house and record.
- Take appropriate monthly water quality samples.
- Check and record static and pumping levels of each well.
- Read all customer meters and compare against total water produced for the month.
- Inspect well heads.
- Lubricate locks.
- Check on-site readings against lab results.
- Confirm submittal of monthly reports.
Annual Tasks
Possible time-of-year for each task is provided in parentheses.
Month | Activities |
January | Overhaul chemical feed pumps, such as O-rings, check valves, and diaphragms. |
Inspect and clean chemical feed lines and solution tanks. | |
Calibrate chemical feed pumps after overhaul. | |
Begin Safety Equipment Repair Log. Maintain log continuously throughout the year. | |
Operate all valves inside the treatment plant and pump house. Maintain log continuously throughout the year. | |
Review emergency response plans. | |
February | Inspect chemical safety equipment and repair or replace as needed. |
Operate all valves inside the treatment plant and pump house. | |
March | Inspect, clean, and repair control panels in pump house and treatment plant. |
Exercise half of all mainline valves. | |
April | Inspect and clean chemical feed lines and solution tanks. |
Calibrate chemical feed pumps. | |
May | Inspect storage tanks for defects and sanitary deficiencies. |
Clean storage tanks if necessary. | |
June | Flush the distribution system and exercise/check all fire hydrant valves. |
Perform preventive maintenance on treatment plant and pump house buildings. | |
July | Inspect and clean chemical feed lines and solution tanks. |
Calibrate chemical feed pumps. | |
Prepare a demand forecast. Identify and evaluate energy conservation measures (for your utility). Identify and evaluate distribution system leaks. Establish/update water loss mitigation program. Establish/update customer incentive program for water-efficient devices. | |
August | Operate all valves inside the treatment plant and pump house. |
September | Exercise mainline valves that were not exercised in March. |
Prepare system for winter operation. This task may be postponed until October or November, depending on local conditions. | |
Make sure unnecessary equipment is properly decommissioned. | |
October | Inspect and clean chemical feed lines and solution tanks. |
Calibrate chemical feed pumps. | |
November | Prepare system for winter operation if not completed in September or October. |
December | Contact an electrician to check running amps on well pumps. |
Operation and Control of Processes
Operational calculations which are theoretical calculations of the working conditions required to compare deviation with actual operations.
- Performance: Ratio (%) between the input and output quantity for any inflow parameter
- Hours of operation of the equipment
- Waste production ratios relative to treated volume (daily, monthly)
- Electrical and reagent consumption ratios relative to treated volume (daily, monthly)
- Hydraulic operation parameters: Tank retention times
- Biological process operational parameters: mass load, volumetric load, sludge age, oxygen required, bulking, foaming, etc.
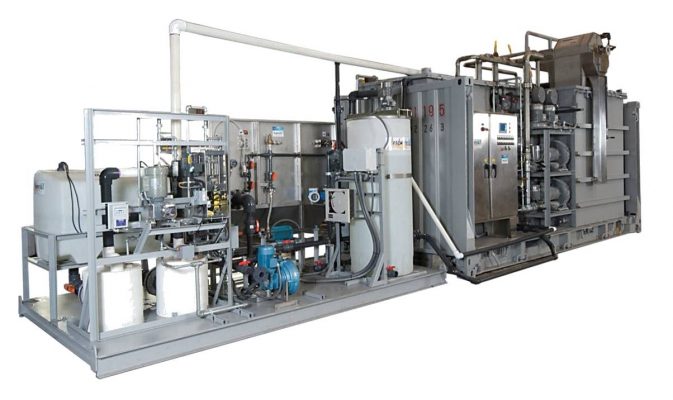
Maintenance Services
Water treatment vendors offer a comprehensive maintenance solution for all facilities, including:
Preventive Electromechanical Maintenance: All operations that are carried out to maintain electrical and mechanical equipment in order to avoid breakdowns and stoppages, reduce corrective maintenance costs and process shutdowns.
Predictive Electromechanical Maintenance: Operations to control the condition of equipment operations in order to predict breakdowns and carry out a rapid repair following a failure. It is based on the ongoing understanding of the condition and operation of the facilities.
Corrective Electromechanical Maintenance: Work to repair equipment, to detect an anomaly or stoppage of equipment and to return it to normal operations.
Metrological Maintenance: Regular calibration and adjustments to continuous measurement equipment and facilities’ instrumentation. Requires a high level of specialization (sensors, flowmeters, etc.)
Regulatory Maintenance: To comply with current regulation for specific equipment, carried out by specialist and authorized companies
Specialized Maintenance: Maintenance of certain types of machinery and systems which due to their complexity or being subject to special regulations require maintenance by specialized companies.
Analytical control: Understanding the parameter values for process waste water (influent, effluent, out-fall, sludge, etc.).
Upkeep: Upkeep of facilities includes all the work required to maintain equipment, civil works, buildings and the remainder of facilities in an adequate state (painting, leaks, carpentry, gardening, rat extermination, etc.).
CTI SUPPLY – Automation System Integrator
As an automation integrator, CTI SUPPLY engineers have been certified to design, program and install PLC, SCADA, HMI automation systems. Our team comprises of well-qualified senior engineers with vast experience in Siemens, Rockwell Automation, Schneider Electric, Honeywell and Yokogawa to name a few. Our team has extensive hands-on experience in high-tech machine, electrical and automation system programming for multinational corporations, high-tech automated manufacturing plants, water and wastewater treatment plants and the oil and gas industry, Furthermore, CTI SUPPLY team has experience with Factory Acceptance Test and Site Acceptance Test.
ALLEN BRADLEY/ROCKWELL AUTOMATION
SIEMENS
MITSUBISHI
SCHNEIDER ELECTRIC
BECKHOFF
OMRON
Are you looking for a system integrator with lower expense on programming cost and better service? Contact us.