Pulp and paper mills are conducive to harsh environments producing lots of dust and heat. Elimination or reduction of the effects of heat and dust is critical to the healthy performance of pulp and paper mills. A preventive maintenance campaign means that equipment failures which result in production downtime and cut profits can be kept to a minimum or even prevented entirely. The top ten tips for ensuring maximum system are available throughout a pulp and paper mill.
Paper production involves lots of sensitive equipment such as scanners and drives. Paper mill foremen could benefit from staying ahead of the maintenance department by taking care to solve potential issues in the mill before they become a hazard. Here are some potential mill issues to be on the look out for.
Contents
1. The Cleanliness Perspective
This is a larger issue than it may first appear. A clean mill is a safe mill, and this is especially true in the paper mill business, as excess dust can affect measurement scanners or cause overheating during the drying process.
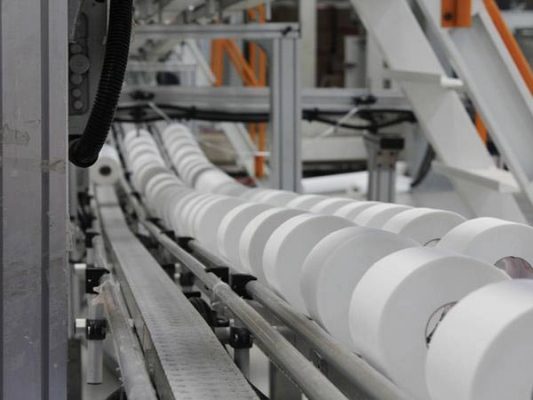
Large quantities of paper dust can also cause many negative health problems for your employees, especially in your maintenance workers who are required to navigate the nooks and crannies of the mill’s machinery. Conducting regular, required cleaning operations can help lessen this issue in the long term. In addition, be certain your employees are always on the look out for obvious spills or other cleaning issues that arise, and notify the sanitation team immediately.
2. Systematic Innovation
A good preventive maintenance schedule is one that is based on first class record keeping. A logbook should track what has been checked; what was found; and any corrective action that was taken. These records form a platform on which to base preventive maintenance schedules.
3. The Equipment Inspection
The importance of this advice will ring true when something breaks in the mill. Your most sensitive devices require regular and constant inspection, be on the lookout for these things:
- Inspect your quality control scanners for window damage or obstruction
- Ensure that your motors and drives are operating at the right temperature
- Listen for odd sounds/noises coming from the machines, chances are an abnormal sound is a maintenance issue
- Check the stock flow and be sure it is fed into the machine un-interrupted
Weekly checks on the quality control scanners can mean inspecting the sensor window material for damage or wear. Early detection of these problems will ensure sensor accuracy and hence more efficient production costs.
Monthly maintenance and verification checks as well as an annual inspection, in addition to regular maintenance on scanners and sensors, are to be carried out to ensure that the scanners and sensors give optimum performance through their entire lifetime.
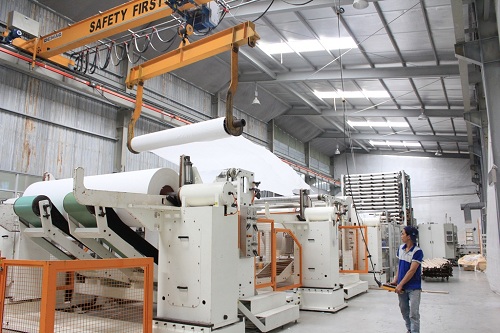
Ideally, equipment should be inspected while operating not only to minimize shutdown time, but also to detect such things as vibration, correct operating pressures and leaks which can not be assessed on stationary equipment.
You’d also be doing yourself a favor by inspecting these problem areas during normal plant operation hours. Moving parts are much more telling when actually moving. You’ll cut down on after hours work this way too.
4. Scanners Maintenance
Scanners and their onboard sensors are fundamental to maintaining quality. The probability that a scanner will fail increases after 3 to 10 years of operation. One of the main reasons for failures is aging of components, but it can be affected by environmental conditions, such as dust and heat and therefore maintenance is key. Preventive maintenance for scanners should involve:
- Visual inspection of the system and its environmental conditions
- Inspection of the connections
- Inspection of the ribbon and fiber optic cables
- Functional inspection of the fan and cooling system
- Inspection of the health pages and alarm history
- Inspection and storage of the parameters
- Functional testing of the system under normal conditions
- Basic measurements with supply voltage
- Inspection of the spare part inventory
- Cleaning of the system
5. Regular maintenance application to drives
Variable speed drives keep the plant moving, so regular preventive maintenance is vital to maintain their health. Keeping drives and motors clean ensures they are within their operating temperatures and helps achieve the best possible efficiency.
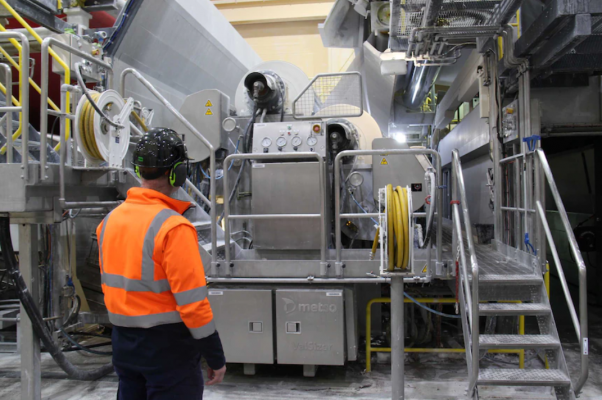
One of the options is to keep an eye on the drives in a plant remotely. This allows such features as drive system parameter verification, parameter changes, on-line measurements, changes to application software, upgrades to system software, remote guidance and written instructions sent to the maintenance PC.
6. Upgrade motors
Motors are another essential in the drive chain and those designed for high reliability will help maintain availability. A new motor for process industries has a 20-30 percent greater cooling surface than its predecessor, reducing the internal temperature considerably. This gives longer component life and will protect motors from overheating. With improved cooling, lubrication intervals are 50 percent longer, as lower temperatures increase the life of the bearing grease.
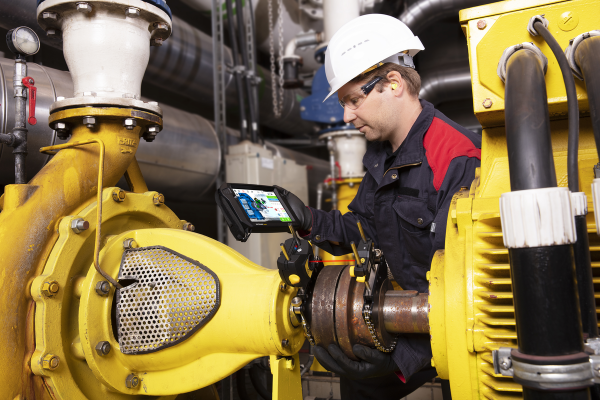
7. The right assignment for maintenance
A key strategy is to control who implements the preventative maintenance procedures and to have an agreed planned program of work. The best results are achieved when specific people with the correct training are given personal ownership.
8. The right training program
Employees should be trained in correct normal operation, so as not to exceed the device’s parameters, and in what to do when problems occur. Shift engineers need the training so they know all about the operation of the system. Training the staff only when the equipment is commissioned and not be concerned about maintaining current training can lead to more call outs to service engineers than needed, resulting in production delays.
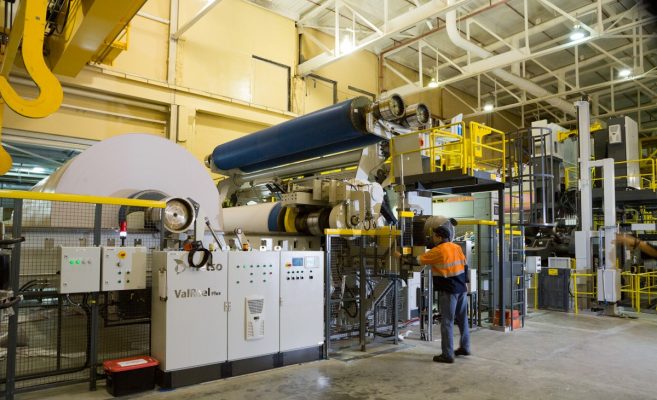
9. Get help outsourcing professionals
Many vendors will also perform on site preventive maintenance. The best vendors will assign dedicated field service engineers to a mill to develop a close relationship with customers. This means that the field engineers are informed about the shutdown schedules so they can plan the more intensive maintenance activities and ensure that the installed base is operating in peak condition.
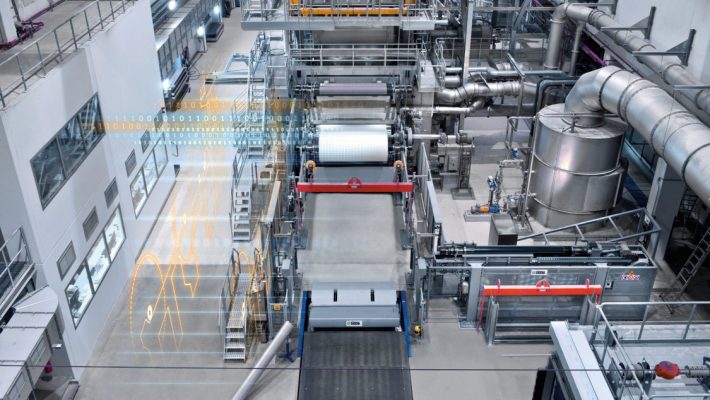
An alternative to performing preventive maintenance on site is to consider sending modules to the vendor’s own workshop. If a module is to be sent to the workshop for repair, it is often practical to perform preventive maintenance at the same time.
10. Standardized development to enhance maintenance
Many companies provide the process and manufacturing industries with a structured program to improve and sustain the performance of production assets.
The best of these arrangements occurs when the client and the vendor work together as a team to develop a business model that supports the client by providing world-class reliability and maintenance services.
Look for a risk / reward performance mechanism that ensures that continuous improvement opportunities are identified and captured over the life of the contract.
A Sample – Paper Mill Succeeds with Outsource Approach to Maintenance
The UPM with former Myllykoski paper mill at Anjalankoski, Finland, produces up to 560,000 tons of uncoated and coated printing paper a year. Myllykoski is a family-owned international paper group with seven mills in Finland, Germany and the United States. The company is one of the largest producers of publication paper in the world.
ABB took over the maintenance operations this Finland located flagship paper mill and quickly achieved some remarkable results with its Full Service concept of plant maintenance.
Explaining why Myllykoski decided to outsource its maintenance operations to ABB, Tuomo Tuomela, executive vice president for technology at the group, says: “We wanted to improve the mill’s performance and efficiency and cut the maintenance costs as well. We looked at all the alternatives and possible partners in maintenance outsourcing and made comparisons. ABB had a good, proven concept on how to take over the maintenance process and implement it successfully. This, and their experience in the pulp and paper industry and strong local presence in Finland, convinced us that they would be successful.”
Within just two years, Myllykoski could register the following improvements:
- Overall equipment effectiveness of the mill’s three paper machines was improved by 0.9 percent, 5 percent and 7 percent, respectively
- Nine different records were set with regard to machine speed and production
- Total annual maintenance costs were reduced by 10 percent, equivalent to savings of $6.8 million during the first two years
- Maintenance-related accidents were reduced by 70 percent in the first year and 66 percent in the second
- The maintenance organization was right-sized by 21 percent during the first two years
Shaft Alignment in CTI SUPPLY
CTI SUPPLY implements laser-based shaft alignment projects for large-load motor drive systems such as crushers, generators, industrial fans and pumps in manufacturing industries such as paper mills, steel, cement and fertilizer.
In particular, the team completed the motor balancing item for a number of paper mills nationwide. According to requirements of the factory, CTI SUPPLY does an actual assessment phase of the machine and carry on the laser alignment.
- Clean the machine and motor base
- Mount and test to identify the deviation via laser aligning device
- Install the vertical and the horizontal aligning shim
Among these plants used the large motor drive system, the problem solving of motor shaft misalignment ensure production progress, minimize machine downtime and saving spare parts costs and energy.