Most companies fail to pursue the strategy of Integrating motor control, automation, and energy systems because of the perceived technical complexities. However, seasoned systems integrators with knowledge in all domains can help plant operators to combine and optimize these systems. Thereby, they can help to drive profitable production.
Motor failure can be expensive as it can cause plant stoppages, damage to equipment, and risk to people or the environment. Robust connection and communication between the motor and the automation system plays an important role in minimizing instances of motor failure. In addition, overall energy costs are reduced when energy data from motors is monitored. On this, function can be better aligned to workload.
In industrial operations, electric motors play a critical role in driving conveyor belts, pumps, compressors, agitators, fans, and other critical infrastructure assets. As the number of motors in process plants increases, management and monitoring of such assets is critical in preventing core process errors such as the proper mixing of ingredients. Motors also account for about 70 percent of the total energy consumed in a process plant. A strategy links motor control, automation, and energy management. Therefore, can help plants to simultaneously reduce costs while increasing production.
Contents
How to Improve Motor Operation and Uptime
Improved motor control operation and uptime can be achieved through several approaches that can be used in tandem with Integrating motor control, automation, and energy systems for performance optimization. Here are some components that can play a role in improving motor reliability, efficiency, and uptime:
Intelligent motor controllers and relay
Relays are electro-mechanical devices that can provide basic functions such as turning the motor on and off. Intelligent motor controllers can provide an automatic means for motor starts and stops, forward or reverse rotation, regulation of speed, limitation of torque, and protection against overloads and electrical faults.
Variable Frequency Drives (VFDs) and soft-starters
These devices fall into the category of intelligent motor starters. Since motors can provide a rich array of performance data, VFDs can interpret this data and aid in failure prevention, in predictive maintenance, and in energy management.
Motor control centers (MCCs)
MCCs allows plant operators to control some or all electric motors from one central location. Such an approach increases reliability, reduces wiring costs, and lowers the risk of human error. In a plant with 100 motors, for example, more than 500 PLC-related I/O with associated wiring will be required. This wiring can be eliminated by connecting an Intelligent MCC to an automation system via a communication bus. The bus itself enables the communication of warnings, alarms, and motor parameters to the automation system.
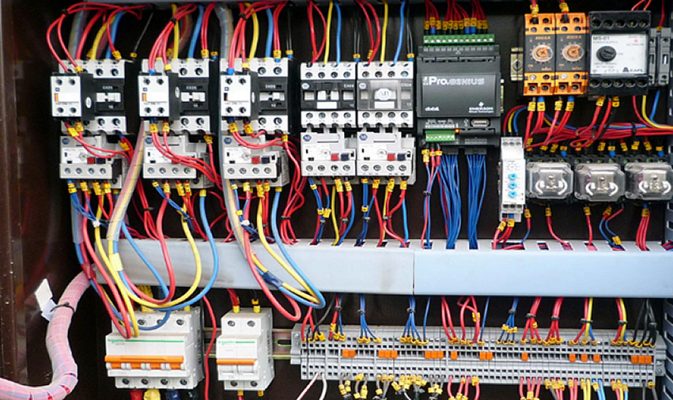
Tips for Optimizing Motor Control Performance
An automation systems integrator for Control System, Hybrid DCS, Intelligent MCC, and EcoXpert, engage in industrial automation systems and energy solution integration projects. Meanwhile, we are often asked to advise the best approach for designing and implementing motor control solutions. Listed below are some important hints and tips for deriving the full benefit from MCC-related investments:
Ensure intelligent MCCs are configured for proper communication in automation systems
An intelligent MCC is much more than just a metal box with electronics inside. In the digital solution era, where data plays a critical role in optimizing operations, the value of the intelligent devices inside the panel is what really counts. The components are intelligent and hence require configuration. Many panel builders do not possess these skills and they often produce panels that can run the motors in local mode but cannot communicate with automation systems. Such a situation (inadequate communications configuration) can cause costly delays during plant commissioning. Users should ensure that the systems integrator who designs and configures the MCC has the expertise, track record, and certification from the manufacturer to perform the necessary work.
Choose the bus component that best meets your factory floor need
Three levels of buses are available for communication back to the automation system–Modbus (RS-485), Profibus or Canopen, and Ethernet.
- Modbus is less expensive but is not recommended for motor control applications because of its slow speed. It is acceptable for monitoring but not for both monitoring and control.
- Profibus or Canopen can work, but be aware, the speed of these networks reduces when the number of devices connected and the length of the bus increases. They are also prone to electromagnetic noise disturbances unless precautions are taken while laying out communication cables and grounding.
- Ethernet is slightly more expensive but performs the best in terms of speed, data transfer capacity, flexibility, reliability, ease of installation, and resistance to noise. Ethernet devices also have built-in web servers and configuration tools that makes installation, commissioning, and diagnostics easy.
Seize the Opportunity to Integrate Automation and Energy Management
Intelligent motor control provides energy consumption data for each motor. Multifunction meters and intelligent breakers are used for monitoring the quality and quantity of electrical energy. Data from all these devices can be captured by energy monitoring systems such as Schneider Electric’s Power Monitoring Expert (PME) and Power SCADA Operations (PSO). These systems output management information reports and dash boards, which help to significantly reduce energy costs.
Source: Schneider Electric Exchange
CTI SUPPLY – THE RIGHT INDUSTRIAL AUTOMATION SYSTEM INTEGRATOR
CTI SUPPLY built up a group of well-qualified senior engineering teams with a great number of in-house control system experts and automation programmers in Vietnam. We are available to take on different projects in scale, even on short notice, and quickly ramp up by working as an extension of your internal team. Our vast experience allows us to offer custom and application specific training as an added benefit to our clients.
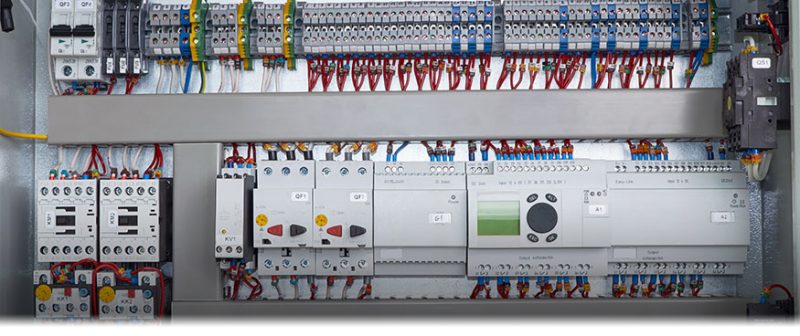
With over years of experience in high-tech machine programming and system control, CTI SUPPLY’s design team are able to simplify PLC/SCADA/HMI prototype process as our main package of your choice. We can also supply you with drawings and documentation for all your equipment builds.
Engineered Solutions | Custom Control Systems | Programming Services
During the current economic uncertainty, CTI SUPPLY is still open for business to offer our full offsite service globally.
Hotline: (+84) 91 190 1717, Email: info@ctisupply.vn