Using Modern Factory Automation and Industry 4.0, any organization can perform processes with little or no human intervention. Automation is able to power a range of equipment, which is then able to fulfil a variety of objectives in a wide array of manufacturing environments.
Contents
Industry Automation
Automation in industrial settings uses a control system and vast quantities of data to manage equipment and processes within a manufacturing environment. Businesses in this industry are always looking for ways to increase output, productivity and efficiency; automation keeps machinery in a specific measured state.
Most automated production lines consist of workstations and a transfer system that moves an item through numerous production phases, using a variety of different tools to change the purpose or appearance of the product in factory automation.
A logic controller oversees this process by managing the sequence in which the machinery is used and the how long each machine must work on the product.
Businesses may use Modern Factory Automation and Industry 4.0 infrastructures for manufacturing, refining and the production of individual parts, as well as the assembly of the final product, where necessary.
Different factory automation systems
There are four different kinds of automation, each serving a specific purpose:
• Flexible Manufacturing Systems (FMS) – Using FMS enables production lines to extend the capabilities of programmable systems to enable changeover with no or minimal lag in production.
• Programmable – Programmable automation allows operations to adapt and reorder the entire manufacturing process to account for deviation in the finished product. This solution will commonly utilise numerical control machine tools run through computer programmes to produce different batches of whatever the deviation needs to be.
• Rigid, Fixed or Hard – As the name suggests, these systems are fixed throughout the production process and cannot be changed without considerable upheaval. This output is generally limited to production lines producing single items in high volume, such as car manufacturing.
• Computer-Integrated Manufacturing (CIM) – Computer-integrated manufacturing systems encompass all factory-related automation and production processes that rely on a computer system. CIM systems will most commonly include the following:
– Automated cranes and transfer systems;
– Numerical control machine tools;
– CAD and CAM integration;
– Computer-aided planning;
– Computer-aided scheduling and production;
– Machine systems;
– Robotics.
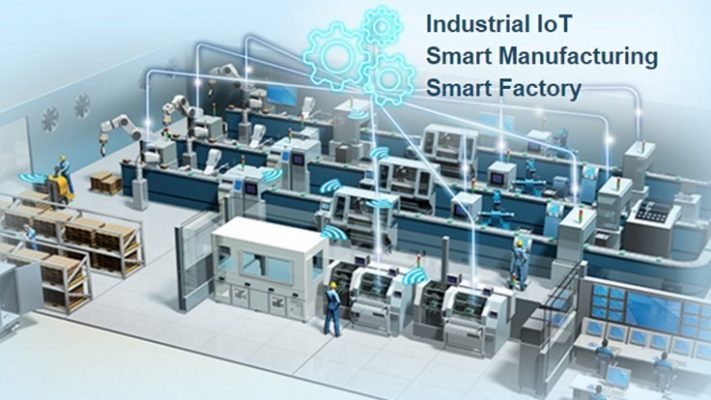
Industry 4.0 in Factory Automation
Industry 4.0, also known as the fourth industrial revolution, or simply smart manufacturing, is the use of automation and data sets in a manufacturing scenario. This highly intuitive and interconnected process enables production lines to meet the requirements of an ever-changing industry.
Within the confines of an Industry 4.0 setting, any standalone activity can now be connected with every other process with increasing speed and accuracy — thereby adding value to the entire operation.
Industry 4.0 is made up of the ‘Nine Pillars of Technological Advancement’, which we’ll talk about in more detail below:
• Pillar 1: Additive Manufacturing
Additive manufacturing is another term for 3D printing, which creates products using 3D technology by creating layers that form an entire object. This technology is commonly used for small batches of custom products, lightweight machine parts and prototype work in factory automation.
• Pillar 2: Augmented Reality (AR)
AR is perfect for pinpointing problems within a machine, and for training and diagnostic purposes.
• Pillar 3: Autonomous Robotics
Robotics has the ability to change their core objectives based on which stage the production is at. In addition to working safely in a human-made environment, robots are also capable of communicating with each other.
• Pillar 4: Big Data & Analytics
Large amounts of data and analytical resource is required to produce the efficiency that every business craves. Production lines can collect data at each stage of the chain to improve their processes and redeploy resources where they see fit.
• Pillar 5: The Cloud
Manufacturing requires collaboration that goes beyond the confines of the company premises. It means that fast, cloud computing is necessary for data collection, analysis, storage and monitoring.
• Pillar 6: Cyber Security
Industry 4.0 is all about moving away from traditionally closed processes into a more contemporary and connected environment. However, this requires more sophisticated levels of user-access and greater reliance on network cyber security.
• Pillar 7: Horizontal & Vertical System Integration
Systems integration is the complete harmonisation of every asset along the supply chain. For instance, a production line manager may wish to keep tabs on other areas of the supply chain, such as information from retail organisations or manufacturing departments.
• Pillar 8: Internet of Things (IoT)
IoT sensors are present within many assets along the production line and in the control centres. These assets will then be able to communicate with each other to offer production staff an in-depth insight into production line operation. This is then sent to the cloud and used in predictive maintenance.
• Pillar 9: Simulation
3D simulations of products, materials, and procedures can utilise real-time data, which is then used to convert it into a virtual model of the entire production operation.
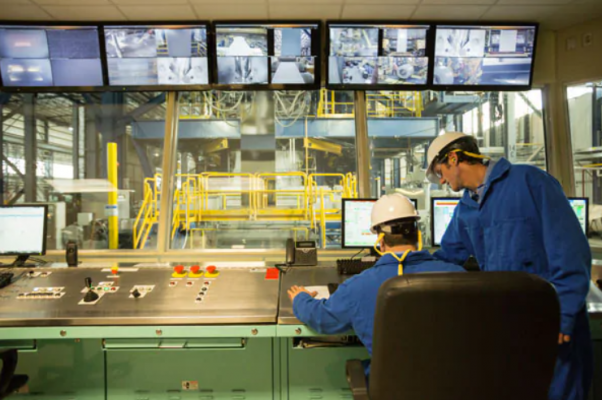
Conclusion
Automation is so effective because it increases quality, output and efficiency by reducing human assistance, thereby dramatically slashing the risk of error. In its most basic form, automation utilises a controller. It assesses a measured state against a predetermined list of values to maintain the desired environments and conditions necessary for efficiency.
CTI SUPPLY – THE RIGHT INDUSTRIAL AUTOMATION SYSTEM INTEGRATOR
CTI SUPPLY built up a group of well-qualified senior engineering teams with a great number of in-house experts and factory automation programmers in Vietnam. We are available to take on different projects in scale, even on short notice, and quickly ramp up by working as an extension of your internal team. Our vast experience allows us to offer custom and application specific training as an added benefit to our clients.
With over years of experience in high-tech machine programming, CTI SUPPLY’s design team are able to simplify control system prototype process as our main package of your choice. We can also supply you with drawings and documentation for all your equipment builds.
Engineered Solutions | Custom Control Systems | Programming Services
During the current economic uncertainty, CTI SUPPLY is still open for business to offer our full offsite service globally.
Hotline: (+84) 91 190 1717, Email: info@ctisupply.vn