Contents
Connecting Rockwell and Siemens Automation System
After engaging in many difficult market competitions over the years, the industry has changed. No longer is there one Programmable Controller and one vendor for a manufacturing system. Machines have multiple sections sometimes with multiple controllers in each section. Machine sections are bought and integrated based on specific features and characteristics. And a lot of the time now, the main controllers might be from Siemens while sections of the machine might use AB Controllers. Or the reverse might be true; main machine control from Allen-Bradley controllers with sections of the machine controlled by Siemens PLCs. This paper focuses on the different ways to make that kind of interoperability and describes the tools that connect the controllers of these two main companies in Connecting Rockwell and Siemens Automation System.
Siemens Controllers
Overview of Siemens Automation System
Trying to describe the Siemens line of controllers (SIMATIC) is like a quick summary of the birds that visit the feeders in my back yard; there are some that show up every day but you can count on something new every day too. The SIMATIC portfolio ranges from small controllers for simple logic tasks to highly complex system solutions. You can get micro controllers, classic Programmable Controllers, PC Controllers, integrated HMI Controllers and Embedded controllers.
Data Table Organization of Siemens Automation System
One of the keys to interoperability between different controller manufacturers is the data table organization.
Every Programmable Controller vendor does this differently and it’s been a nightmare since day one. Every time you move from one PLC to another you have to learn the mnemonics of how the next controller structures its data table.
In the Siemens world, a data table is constructed from a set of defined types. The available types vary slightly from controller to controller while the number of data items is vastly different throughout the SIMATIC line.
Here is the list of typically supported data types for a Siemens PLC:
Elements of a data table are accessed by combining the mnemonic for the type with the offset into the data table for that type. IW502 is the 502nd Input Word in the data table while Q10 is the tenth Output Bit.
The number of data items found in a controller varies with the controller. For example, there may be no Input Double Words in one controller and 65535 in another. It all depends on the target application for that controller. A small, low cost controller for machine builders may have a lot fewer double words than a controller designed to control an entire papermaking converting line.
Connecting Siemens PLCs to Rockwell Automation Controllers is largely a matter of connecting data in the Siemens data table to the data table of the RA Controller in connecting Rockwell and Siemens Automation System.
Communication Interfaces – Protocols & Communication Ports in Siemens Automation System
There are a number of ways to access those internal data items of a Siemens PLC. As with everything else, some PLCs will support one mechanism while others may support two or more different mechanisms. The following sections describe the communication interfaces you may find on a Siemens Programmable Controller in Rockwell and Siemens Automation System.
Serial Communications
Except for one or two models, serial communications is available through an add-on module for all Siemens controllers. The port connects the Controller to barcode readers, printers, operator interfaces and other SI-MATIC Controllers. RS232, RS422 and EIA-485, formerly RS-485 can be used in Siemens Automation System.
Devices can be accessed using a variety of protocols including simple ASCII, Modbus RTU Master/Slave, 3964, and RK512. Modbus RTU, 3964 and RK512, are binary protocols that can be used with devices that need to exchange binary device data with a controller. These protocols can also be used for Simatic Controller to Controller communication.
MPI Communications
MPI is a multi-node network used for Programming and SIMATIC Controller to Controller communication. An MPI interface is integrated on CPUs of the modular SIMATIC controllers. There are no MPI interfaces on the S7-1200 and S7-1500.
MPI Communications are proprietary communications that S7 Controllers use to exchange data between each other and other Siemens products. MPI communications use S7 Basic Communication, S7 Communication and Global Data Communication.
The S7 Protocol is a proprietary protocol that facilitates the transfer of data from one Siemens controller to an-other. The S7 Protocol is a subset of Profibus DP and uses many of the same commands as Profibus DP. In fact, some users have tried to use S7 Controllers as nodes on a Profibus network. This configuration is not supported by Siemens automation system and may not work properly. An adapter is recommended in those applications in which you want to connect the MPI port to a Profibus network in Siemens Automation System.
There are a few off-the-shelf products from third party manufacturers that allow other kinds of devices to communicate on MPI channels.
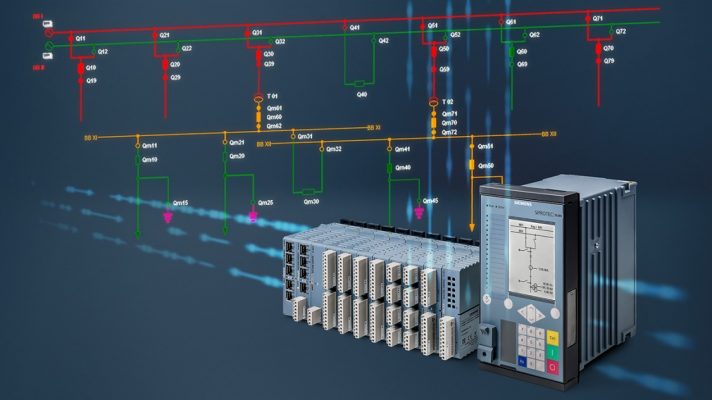
Profibus DP
Profibus was born out of a combined push by the German government, German companies, and other industry leaders in the late 1980s. Profibus defines an RS485 serial physical layer with special drivers to obtain speeds as fast as 12MB. A standard twisted-pair wiring system is typical but Profibus can also be implemented with fiber-optic and other media.
Profibus is a smart, sensor-bus technology. Slave devices on the system connect to a central controller, usually a SIMATIC S7 Programmable Logic Controller. Once connected, the S7 Controller sends outputs to these devices and receives inputs from them.
Profibus had two huge advantages over other sensor bus technologies. One is speed and the second is data size. 12Meg is really fast. Faster than most people need but generally automation engineers believe that when possible, it’s always best to go faster. Speed has its downside though and that’s cost. It costs more to go that fast. A special ASIC with the communications infrastructure on it (MAC – Media Access Controller), special transceivers, cabling and connectors all make Profibus devices significantly costlier.
The data size advantage over DeviceNet is significant. Profibus has a frame size of 244 bytes. That’s monstrous compared to 8 byte frames in CAN. Yes – DeviceNet has fragmentation but that eats up so much band-width it is hardly useable in Siemen automation systems.
One of the things some people dislike about Profibus is the data representation. All Profibus devices look like a rack of I/O to the controller. That means that a device is a series of slots, each slot with a module in it and all sorts of different size modules. That’s easy for simple devices like I/O devices. You can simply decide that the first slot has a module that is a 16 bit Discrete Input device. The second is 8 bits of Discrete Output and so on. If you have Analog inputs/outputs too, you could setup the device using four slots and four modules. For other non-IO devices, that’s kind of awkward.
Profinet IO
Profinet IO is very similar to Profibus, but not really Profibus on Ethernet. While Profibus uses cyclic communications to exchange data with Programmable Controllers at a maximum speed of 12Meg baud, Profinet IO us-e’s cyclic data transfer to exchange data with Simatic Programmable Controllers over Ethernet. As with Profibus, a Programmable Controller and a device must both have a prior understanding of the data structure and meaning. In both systems data is organized as slots containing modules with the total number of I/O points for a system with the sum of the I/O points for the individual modules.
Profinet IO uses three different communication channels to exchange data with programmable Controllers and other devices. The standard TCP/IP channel is used for parameterization, configuration and acyclic read/write operations. The RT or Real Time channel is used for standard cyclic data transfer and alarms. RT communications bypass the standard TCP/IP interface to expedite the data exchange with Programmable Controllers. The third channel, Isochronous Real Time (IRT) is the very high speed channel used for Motion Control applications. IRT is implemented using a custom ASIC and is not the subject of this paper.
Types of Profinet IO
Profinet IO classifies devices into three types; IO-Controllers, IO-Devices and IO-Supervisors. IO-Controllers are devices that execute an automation program. Controllers, functionally similar to a Profibus Class 1 Master, exchange data with IO-Devices. IO-Devices are distributed sensor/actuator devices connected to the IO-Controller over Ethernet. In Profibus terms, IO-Devices are similar to Profibus slaves. IO-Supervisors are HMIs, PCs or other commissioning, monitoring or diagnostic analysis devices. These devices are similar to Class 2 Profibus Masters.
IO-Controllers map IO data from Profinet IO devices into the process image of the controller. In Siemens S7 Programmable Controllers, I/O data, alarms and status data is mapped into the process image in much the same way it is done for Profibus devices. These data values are then available for use by the control program. IO-Controllers must support the following kinds of services:
Cyclic Data Exchange – The exchange of data between IO-Controllers and IO-Devices
Acyclic Data Exchange – The exchange of Configuration and Diagnostic data
Alarms – Alarm data exchange from an IO-Device to an IO-Controller
Context Management – Connection processing

CTI SUPPLY – THE RIGHT INDUSTRIAL AUTOMATION SYSTEM INTEGRATOR
CTI SUPPLY built up a group of well-qualified senior engineering teams with a great number of in-house experts and PLC programmers in Vietnam. We are available to take on different projects in scale, even on short notice, and quickly ramp up by working as an extension of your internal team. Our vast experience allows us to offer custom and application specific training as an added benefit to our clients.
With over years of experience in high-tech machine programming, CTI SUPPLY’s design team are able to simplify SCADA prototype process as our main package of your choice. We can also supply you with drawings and documentation for all your equipment builds.
Engineered Solutions | Custom Control Systems | Programming Services
During the current economic uncertainty, CTI SUPPLY is still open for business to offer our full offsite service globally.
Hotline: (+84) 91 190 1717, Email: info@ctisupply.vn